Project: Realization gas-free printing plant by delivery of afterburner
Cervitechnician Andries Kramer has been very closely involved in the expansion of the VIV for the past 3 years. What started 3 years ago with the installation of a new Comexi F2 Flexo 10-color printing press, including the necessary installation work, has led to several new projects in recent years.
For example, a new afterburner, supplied and managed by Cervitech, was commissioned last year. Andries explains: an afterburner from Relox, the brand we represent, is an installation that is well known within industrial waste gas processing installations for its efficient operation. This is visible in the 99.99% cleaning of the drying air and the low concentration required for an autothermal process.
This year, in consultation with the customer, it was decided to install heat exchangers in the existing flexo presses, the afterburner was already installed. Andries says by placing these heat exchangers, the total printing process becomes a lot more environmentally friendly and it gives our customer enormous savings on gas costs. With the correct adjustment of printing presses in combination with a certain type of shift work, gas consumption is drastically reduced, optimally even without gas.
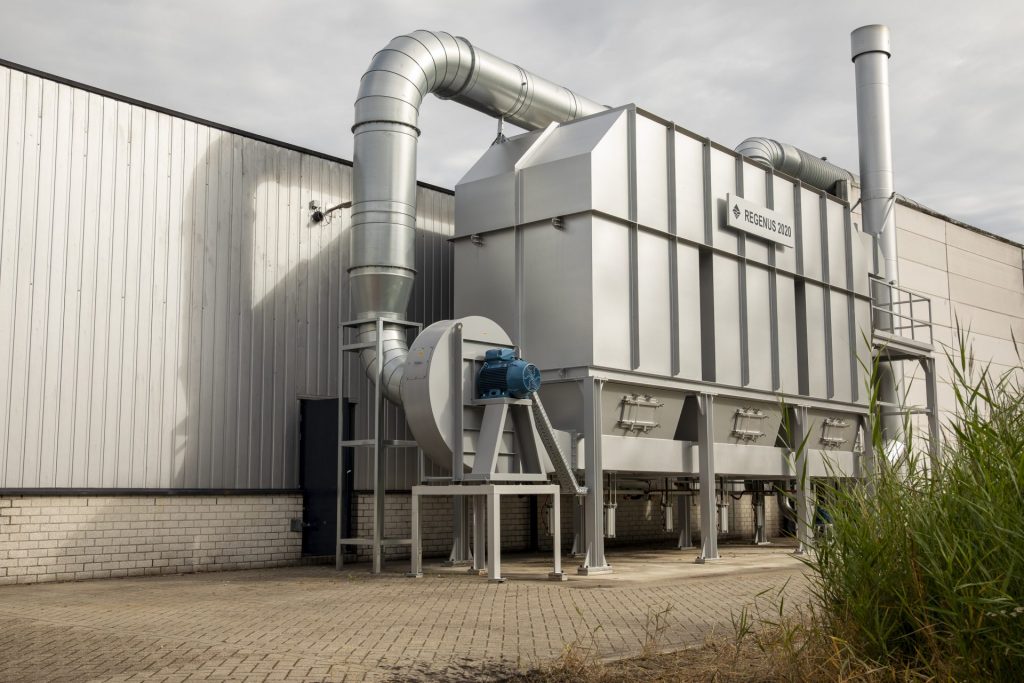
Previously, the released heat / energy was emitted in the afterburner process. (The installation temperature is between 750 and 1000 degrees Celsius). Now the surplus of heat is used through a heat exchanger, which heats water to a maximum of 100 degrees. This heat is used to heat the drying air of the printing presses and to heat offices and production areas.
Before Cervitech starts such a project, we discuss all steps in the process with our customer, project managers and suppliers. For example, we went with the customer to our supplier of the printing press in Spain to agree on what the right specializations of the machine should be, we guide and involve our customer and partners from A to Z in the process.
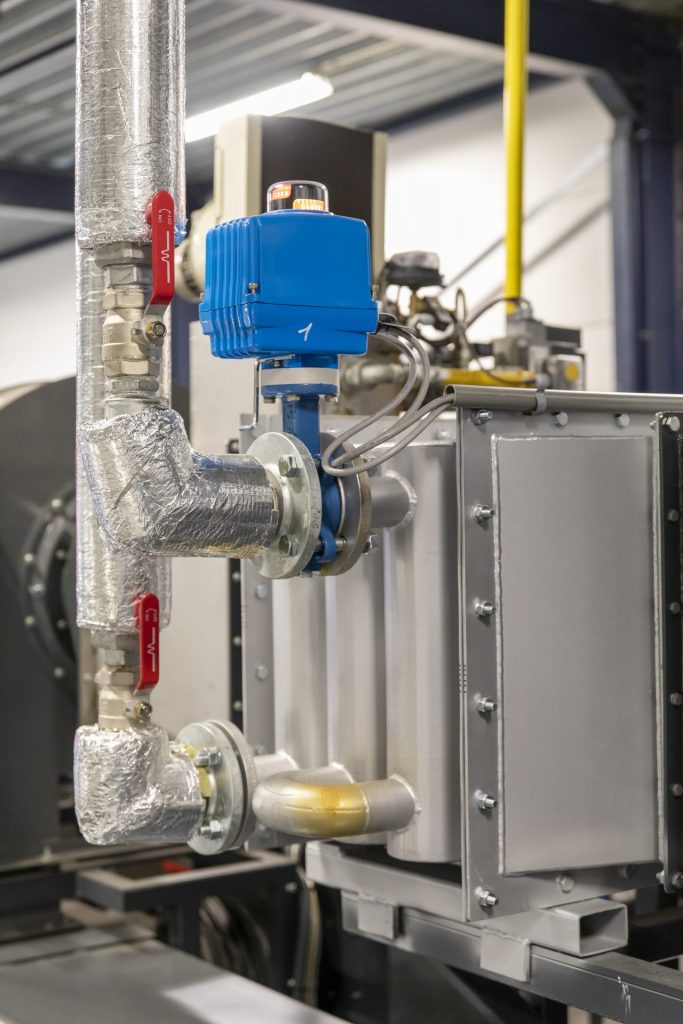
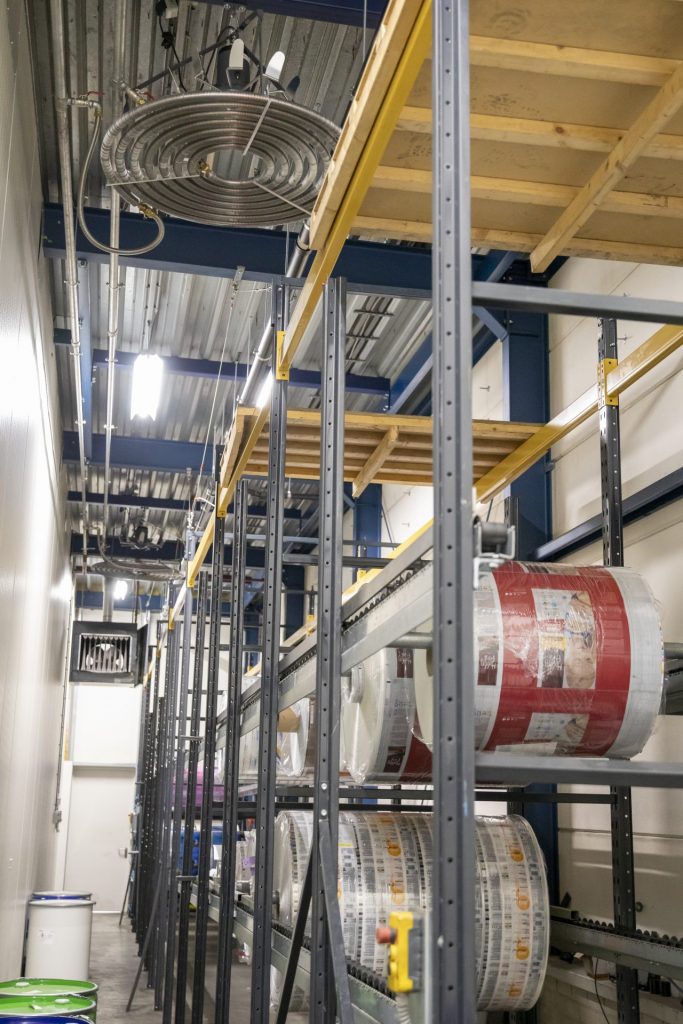
Together with our measurement technicians Harm and Hylke, we also carried out measurements in a number of very extensive sessions of, among other things, the drying air flows with solvents and the air flow rate. We process this data in a very accurately substantiated report for the customer, with sound advice on how to deal with it. Project manager Klaas explains that we are now writing more and more advisory reports of this kind for both the end user and also many for the environmental services of the province!
Andries continues within the overall project we work together with permanent partners. For example, RELOX supplied a new 20,000 m3/h afterburner, with the installation work for inside and outside being carried out by our permanent Partner Holtrop and Jansma from Dokkum.
All in all, Weinand van Kesteren director of the VIV in Veenendaal adds that he is very satisfied with this investment, an investment that will certainly pay for itself!
#VIV-Veenendaal #Emissionreduction
#Afterburner #Relox #Printingcompany #Flexo #Packaging #Solvents #Energyrecovery
#Comexi #FIDmeasurements
#Holtrop&Jansma
#Nutrients